Mastering the art of low volume plastic injection molding: A comprehensive guide for professionals
Low-Volume Plastic Injection Molding: What Is It?
Low-volume injection molds are the process of producing plastic parts in tiny batches, usually fewer than 1000 pieces. Low-volume injection molding with plastic frequently occurs using inadequately calibrated machinery that can be utilized for prototyping, much like low-volume production techniques for metal or wood. Prototypes and functioning components, such as those found in automotive or medical equipment, are the usual forms of low-volume production. The fast-growing industry is currently going through a significant transition. Things have to be sent as soon as possible because of how swiftly this sector moves. It is the responsibility of product engineers, designers, and manufacturers to guarantee that their goods are consistently of high quality. Injection molding in low volumes is one area of manufacturing where customer needs are the focus.
The best manufacturing method for making a component in smaller quantities than 100,000 is low-volume molding process. It is used for mass-producing similar components prior to committing to a long-term mold setup; nevertheless, some low-volume polyester products could never require larger-scale manufacturing, so it is used beforehand. One of the more common methods used to create plastics nowadays is molding. The optimum applications for MPM equipment are modestly produced plastic-molded items. They can employ cheap instruments with a single cavity, are affordable, and need little space. Among other applications, low-volume injection molding robots are perfect for producing ASTM specimens, prototypes, and bridges. Additionally, these devices may fulfill orders for smaller amounts.
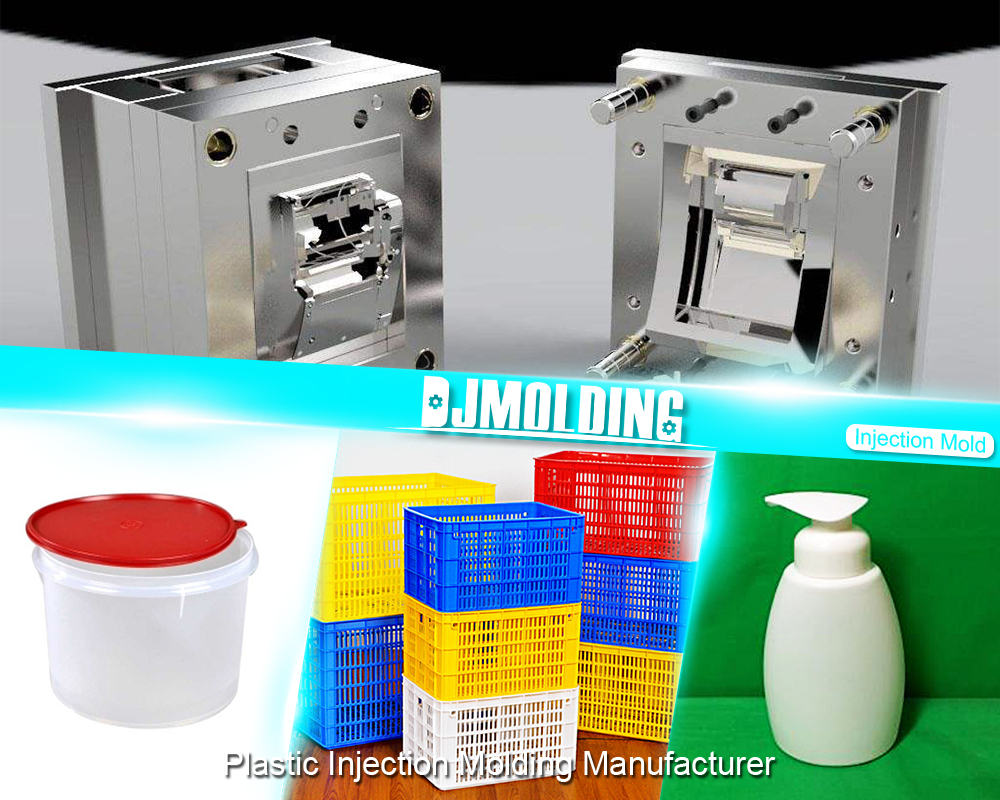
Why Would You Use Low-Volume Plastic Injection Molding?
In the prototype and functional testing phases of product development, low-volume plastic injection casting is usually utilized. End-use parts for limited production runs, like those used by Apple and Tesla, can also be produced by low-volume plastic injection casting.
Applications for low-volume plastics are numerous and include:
Product Development
Prototyping
Minimal Production Volume
Benefits of Injection Molding at Low Volume
Low-Volume Plastic Injection molding can be a vital process in the field of quick production. The ongoing development of the model might shorten lead times for shipping and production. Regretfully, the conventional method does not yield the desired outcomes as rapidly. Nonetheless, the features of the production process conflict with the demands of the plastics market in a number of ways. When the mold structure is complex, the manufacturing time for the parts could increase significantly. On the other hand, low-mass injection casting provides a workable solution for quickly addressing such issues.
For businesses that frequently need to develop prototypes, low-volume injection molding of plastic is an excellent option. Both the automobile and medical industries may fall into this category. Businesses wishing to make small batches (usually fewer than one thousand pieces) of products sometimes look for low-volume manufacturing services. Low-volume manufacturing facilities can also be advantageous for companies seeking a more affordable option than the hefty upfront expenses linked with conventional rubber injection molding.
Just a handful of its many benefits are as follows:
Uses Tooling Made of Softer Aluminum
Unlike the conventional molding process, low-volume injection molding eliminates the need for a hardened steel casting tool system. Instead, it uses aluminum, which is easier to mold into the desired shape. The hardness of aluminum is significantly less than that of steel. It significantly reduces complexity and facilitates speedy, simple use. When aluminum is utilized for tooling, the annealing step of the heat treatment procedure might be omitted to expedite it. In order to adequately harden the metal and release internal tensions, steel tools frequently require annealing. Despite these, aluminum molding systems can benefit from the majority of surface procedures that are applied to steel molds.
High-quality Parts Production
Low-volume injection molds can produce longer-lasting and more functional products, even though the tooling material is softer. Numerous things can be assembled using this production approach. Moreover, aluminum conducts heat transfer to steel much more quickly unlike steel. Increased conductive power can make the precise placement of the coolant lines unnecessary. In this manner, more mold might grow. So, low-volume injection molding systems offer greater design flexibility, bridging the space inbetween the mass production and prototype.
Modularity in Design
The goal of small-scale injection molding is to create fewer pieces in a shorter amount of time. Because of this, a company’s decision to make little alterations or modifications to the design won’t have a big effect. Before the product is delivered to the customer, it can be improved iteratively using this process. Superior injection molding of plastic provides instant feedback, hence enhancing the product’s manufacturability. It makes it possible to test novel concepts across a range of sectors prior to the need for expensive mass manufacturing.
Overpass for Scale
A corporation should begin small-scale plastic manufacturing if it intends to eventually make its products in huge quantities. It facilitates the move from prototype to large-scale manufacturing. With this technique, a prototype that can be produced in large quantities can now be created. Beyond that, it enhances the process as well as the final product.
Low-Volume Plastic: What Is It?
Low-volume plastics are generally utilized in the product development and prototyping stages, so that before parts manufactured by small-scale injection molding machines are put into full production, they can be checked for fit and functionality. Low-volume materials are created specifically for the item being sold and are frequently not offered at retail establishments. Low-volume polymers are helpful in development and prototype procedures where fit is crucial because they are frequently created with high degrees of detail.
Which Polymers Are Employed in Inject Molding?
The following plastics are most frequently employed for the low-capacity plastic injection molding:
polymer (PMMA)
Butadiene acrylonitrile styrene (ABS)
nylon polyamide, polycarbonate, polyethylene, polyoxymethylene, polypropylene, polystyrene, and polyethylene (PE, PE, POM, PS)
TPE, or thermoplastic elastomer
TPU, or thermoplastic polyurethane
Because ABS is strong and long-lasting, many businesses utilize it to make low-volume plastic injection molds. Numerous products, including medical equipment and devices as well as automotive parts, can be made with ABS. Nevertheless, a wide range of plastics can be used with low-volume injection molds.
Other popular low-volume injection molding polymers are nylon, PPSF, and polycarbonate (PC). While these polymers are just as strong and long-lasting as ABS polymers, they also have distinct characteristics. Because it can withstand a wide range of chemicals, nylon is perfect for use in medical manufacturing applications. When choosing materials for parts that must withstand harsh chemical environments, nylon is an excellent option.
Which low-volume polymer is best for me?
Whether you are producing or prototyping will determine what kind of low-volume plastic you need to utilize. Acrylic plastics are reasonably priced, multipurpose, and incredibly simple to deal with. Yet, they are more expensive and prone to scratches than glass. Its operating temperature is also too low for certain industrial uses. Although it costs more than acrylic, ABS is an engineering-grade polyethylene that is stronger and more rigid.
Additionally, because of its higher operating temperature range of up to 100°C (212°F), it is appropriate for industrial applications where frequent contact with high temperatures is necessary for regular operation. Due to its strength and inherent transparency, polycarbonate is a good choice for applications requiring exceptional dimensional stability and optical clarity. It has strong impact strength and may retain its physical characteristics at high temperatures.
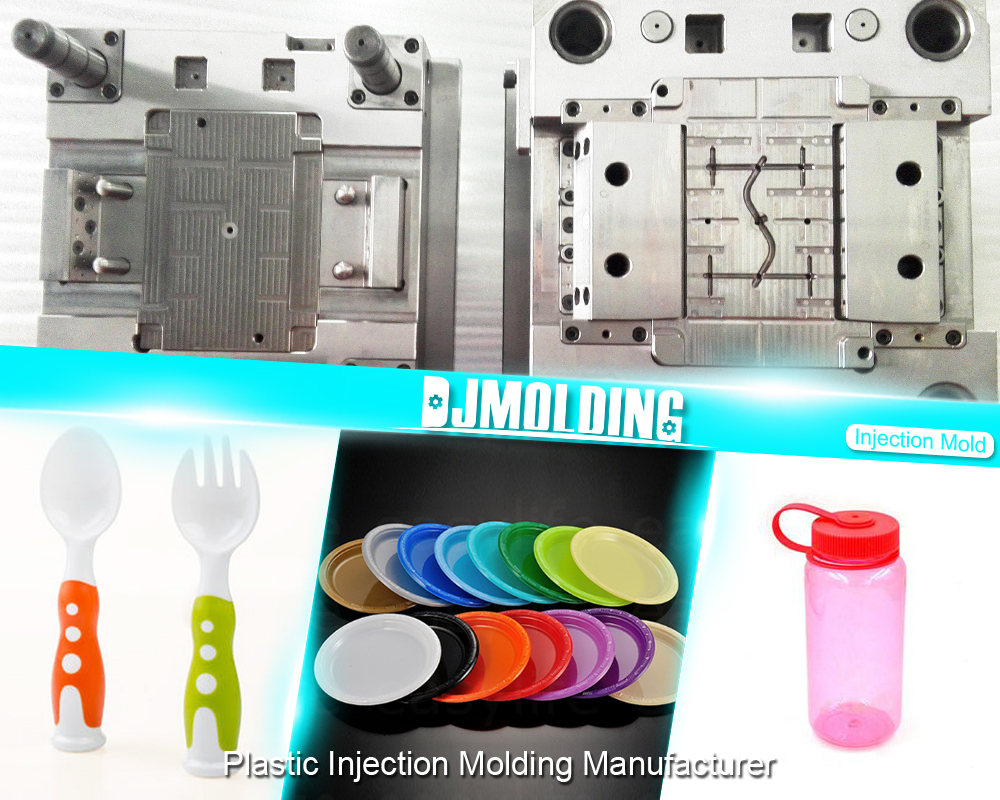
How Low-Volume Plastic Molding by Injection Can Be Started
Having the right tools is the first step towards starting a low-volume plastic injection molding business. New molds must be used for low-volume injection molding; these can be obtained online or at your neighborhood machine shop. In order to test the molding procedure, a prototype must also be made. In theory, low-volume plastic injection molding seems pretty straightforward, but there are several subtleties that, depending on how effectively they’re done, could make or break your product.
You’ll need to deliver your low-volume plastic injection molding prototype to a seasoned injection molding firm when it has been successfully made. Because it might be costly to redo plastic injection molds if they don’t work out as planned, it is imperative that you pick a reputable source.
For more about mastering the art of low volume plastic injection molding: A comprehensive guide for professionals,you can pay a visit to Djmolding at https://www.djmolding.com/low-volume-injection-molding/ for more info.