What Are The Advantages And Disadvantages Of Injection Moulding?
What Are The Advantages And Disadvantages Of Injection Moulding?
Injection moulding is a manufacturing process that involves the production of parts and products by injecting molten material into a mould. The molten material is typically a thermoplastic or thermosetting polymer that is heated and then injected under high pressure into a mould cavity. Once the material cools and becomes solid, the mould opens, and the output is ejected. This process has revolutionized the manufacturing industry for many good reasons.
Initially, this process was used to produce simple items such as buttons and combs. However, with technology and materials advancements, injection moulding has become a widely used manufacturing method for producing various products across various industries.
Advantages of Injection Moulding
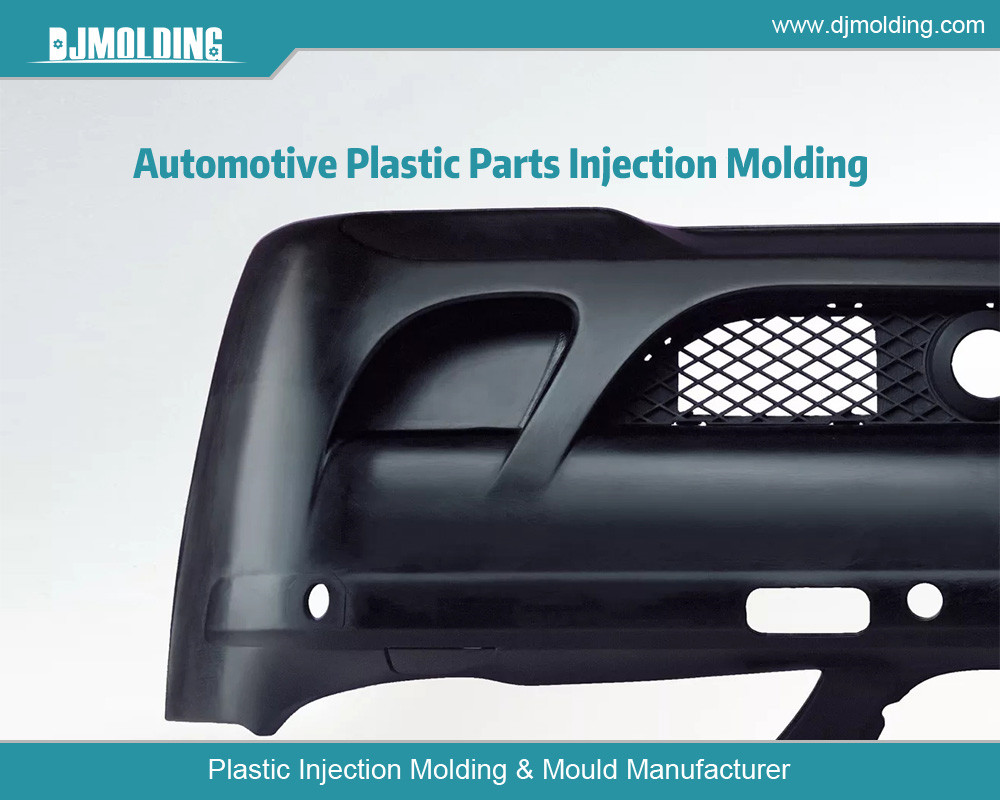
High Production Efficiency
Injection moulding achieves high production efficiency through several key factors. Firstly, the use of automated machinery allows for continuous production cycles with minimal downtime. The machines are designed to operate at high speeds, injecting molten material into mould cavities rapidly. This results in shorter cycle times and increased output rates compared to manual or semi-automated processes.
Moreover, injection moulding machines can be equipped with multiple cavities or molds, allowing for the simultaneous production of multiple parts in each cycle. This further enhances production efficiency by maximizing the utilization of the machine’s capabilities. Additionally, the ability to use hot runners, which are channels that keep the material molten between the injection unit and the mould cavity, reduces material waste and cycle times.
Cost-Effective Manufacturing Process
Injection moulding is a cost-effective manufacturing process due to several factors. Firstly, the high production efficiency mentioned earlier leads to reduced labor costs per part produced. The use of automated machinery eliminates the need for extensive manual labor, resulting in lower production costs. Additionally, the machines can operate continuously with minimal supervision, further reducing labor expenses.
Furthermore, injection moulding minimizes the risk of human error, which can lead to defective parts and rework. The automated nature of the process ensures consistent quality and precision, reducing the need for additional work or scrap. This results in cost savings by eliminating the time and resources required to rectify defects.
Versatility in Design and Material Selection
Injection moulding offers unparalleled versatility in design and material selection, making it suitable for a wide range of applications. The process allows for the production of complex part geometries with intricate details that are difficult to achieve with other manufacturing methods. This is possible due to the ability to create molds with intricate cavities and features.
Moreover, injection moulding supports a wide range of materials, including various thermoplastics and thermosetting polymers. Each material has its own unique properties, such as strength, flexibility, or chemical resistance. Manufacturers can choose the most suitable material for their specific application, considering factors such as the intended use, environment, and desired performance characteristics.
Consistent Quality and Precision
Injection moulding achieves consistent quality and precision in the produced parts through several key factors. Firstly, the use of automated machinery ensures controlled processes that minimize variations in part dimensions and characteristics. The machines are programmed to follow precise instructions, resulting in parts that meet strict specifications consistently.
Additionally, injection moulding allows for tight tolerances, enabling the production of precise parts that fit together seamlessly. The molds used in injection moulding are designed with high precision to ensure accurate replication of part geometries. This level of precision is difficult to achieve with other manufacturing processes.
Reduced Waste and Environmental Impact
Injection moulding is an environmentally friendly manufacturing process that reduces waste and minimizes its impact on the environment. The process generates minimal scrap as excess material can be recycled and reused. This reduces material costs and waste disposal expenses, making injection moulding a sustainable manufacturing solution.
Furthermore, the ability to use recyclable materials promotes environmental sustainability by reducing the consumption of virgin resources. Many thermoplastics used in injection moulding can be recycled multiple times without significant degradation in performance. This reduces the demand for new materials and contributes to a more circular economy.
Disadvantages of Injection Moulding
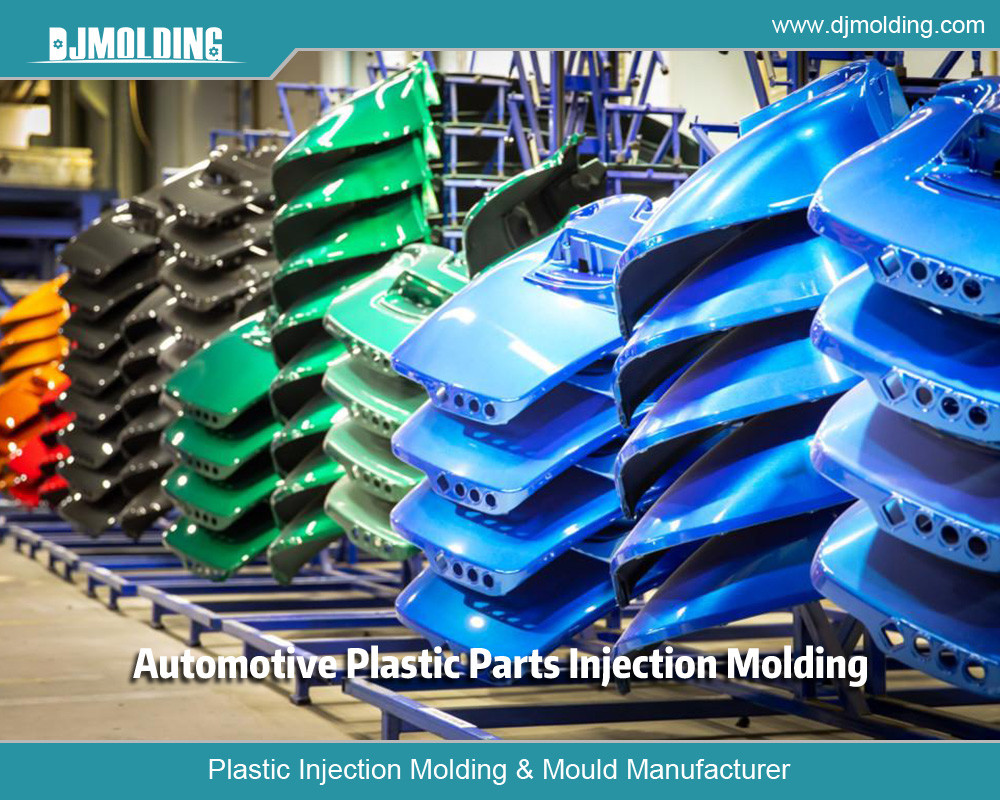
High Initial Investment and Tooling Costs
One of the main disadvantages of injection moulding is the high initial investment required. The cost of purchasing and setting up injection moulding machines, molds, and auxiliary equipment can be significant. Injection moulding machines come in various sizes and configurations, with prices ranging from thousands to millions of dollars depending on their capabilities.
Additionally, the design and fabrication of molds can be expensive, especially for complex parts or large production volumes. Molds are typically made from high-quality steel or aluminum alloys to withstand the high pressures and temperatures involved in the injection moulding process. The complexity of the part geometry and the number of cavities in the mold also affect the cost.
Limited Flexibility in Small-Scale Production
While injection moulding is highly efficient for high-volume production, it has limited flexibility in small-scale production. The setup and preparation time required for each production run make it less suitable for small-scale or custom production.
Changing molds or materials can be time-consuming and costly. Each mold is designed specifically for a particular part geometry, and changing molds requires disassembling and reassembling the injection moulding machine. This process can take several hours or even days, depending on the complexity of the mold and the machine setup.
Potential for Defects and Quality Control Issues
Despite its ability to achieve consistent quality and precision, injection moulding is not immune to defects and quality control issues. Several factors can contribute to the potential for defects and quality control issues in injection moulding.
Material variations can affect the properties and performance of the final product. Even with strict quality control measures, variations in material composition or processing conditions can lead to inconsistencies in part dimensions, strength, or appearance. It is crucial to work closely with material suppliers and conduct regular testing to ensure consistent material quality.
Mold wear is another factor that can impact part quality. Over time, the repeated injection of molten material into the mold can cause wear and tear on the mold surfaces. This can result in dimensional variations or surface defects in the produced parts. Regular maintenance and mold refurbishment are necessary to minimize these issues.
Final Words
In conclusion, injection moulding is a highly efficient and cost-effective manufacturing process that offers numerous advantages for producing a wide range of products. Its ability to create complex shapes, high precision, and consistency make it a popular choice for industries such as automotive, medical, electronics, and consumer goods. With advancements in technology and materials, injection moulding continues to evolve, providing even more opportunities for innovation and customization.
For more about the advantages and disadvantages of plastic injection moulding,you can pay a visit to Djmolding at https://www.djmolding.com/the-advantages-and-disadvantages-of-plastic-injection-molding/ for more info.