What Is Low Volume Injection Molding?
What Is Low Volume Injection Molding?
Low-volume injection molding is an indispensable process when it comes to manufacturing. With its ability to efficiently deliver small-scale plastic parts and provide a pocket-friendly approach, it keeps businesses of all sizes well within their budgets – prototyping, testing, or low production runs without needing costly tools and complex lead times.
Molten plastic gets injected into a mold cavity that hardens and solidifies in no time before it’s ejected as an excellent finished product from that same mold. Nothing can surpass the utility of this particular technique for those who frequently change designs or carry out restricted productions.
Thus, what may have posed difficulty otherwise can be taken care of quickly by going with low-volume injection molding, which produces high-quality results while saving on precious costs and timing.
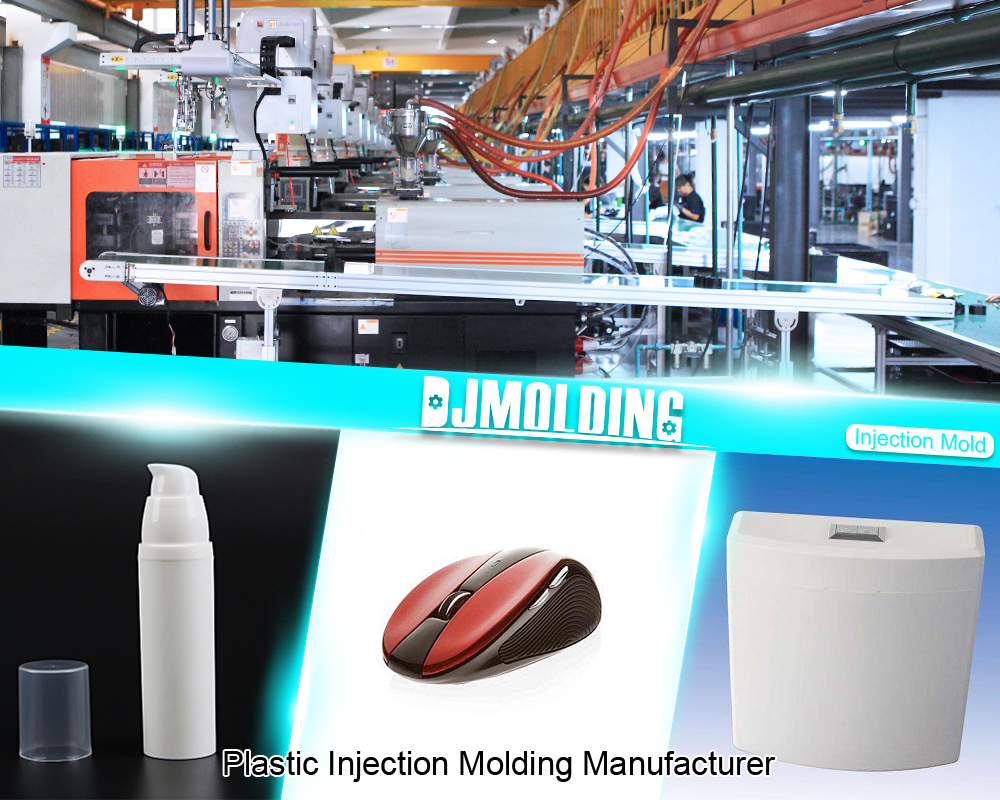
Advantages of Low-Volume Injection Molding
One of the biggest perks of low-volume injection molding is its affordability — perfect for businesses whose production volumes are small. That’s because you don’t have to manage expensive tooling like you would with traditional injection molding. So, if your budget isn’t too big, but you need parts quickly! Low-volume injection molding comes in handy.
Plus, it gives those same companies even better response times than usual since setup and producing parts don’t take as long without the need for tool use beforehand. For projects that require an extra jolt of speed or just a tighter timeline? This method is excellent.
The end product leaves nothing to be desired quality-wise: thanks to careful control when injecting precisely hot plastic into pieces, every part meets the required specs exactly — something doctors and astronauts definitely appreciate when tight tolerances matter most.
Who can beat this kind of flexibility in design changes? There is no need to respecify pricey tools so firms can rapidly make improvements (and keep making new ones!) as needed without any added costs incurred along the way, leading to superior final products.
Materials Used in Low-Volume Injection Molding
When it comes to low-volume injection molding, the type of material you use can make or break your project’s success. Among the most common materials used for this purpose are thermoplastics such as ABS, polycarbonate, polypropylene, and nylon – all offering different levels of properties, including strength, elasticity, and resistance to heat and chemicals.
However, other essential factors need to be considered when picking out the suitable material: mechanical property requirements like durability and flexibility, environmental conditions in which the part will be employed, not to mention cost-effectiveness, and legal obligations that must be met. Minor details may seem unimportant, but if overlooked, they can cause massive problems down the line.
The Process of Low Volume Injection Molding
Involving several meticulous steps, low-volume injection molding is no easy feat. To begin with, the mold has to be prepped for its duty by being scoped off of any particles and brought warm to make sure it holds the plastic securely.
Subsequently, it’s clutched tight while molten plastic streams in at wave-like intensity, causing an exothermic reaction that solidifies the material. Once it liquefies again due to a temperature change occurring during the opening of said clamps, the finished article will pop out.
To implement this process, various tools are used – injection machines housing hoppers for pellet supply and a barrel where those same pellets get their liquid transformations quickened by way of a spring or forceps direct setup into molds primarily fashioned from steel or aluminum but precisely machined so they receive all itemized demands.
Last but not least, top quality control measures must be taken into account before production begins, with eyes open, watching over every single step done along the way until each part is checked off as ticked in conformity, stemming from fulfilled specs, etc.
Design Considerations for Low-Volume Injection Molding
Design can make or break a successful low-volume injection molding project. It’s vital to consider all the specific needs of your part, craft it accordingly, and bear in mind the unique elements that go into injection molding: wall thicknesses, design angles, rib placement, bosses – you name it!
To efficiently get things done when undergoing low-volume injection molding production, uniform wall thickness should be maintained at all points, which consequently ensures an effective tank-filling of each cavity plus prevents warping or sink marks from occurring.
Plus, incorporating draft angles allows for quick and effortless ejection of components from molds. When designing ribs, aim to balance out, creating enough strength and rigidity while avoiding causing any molded issues as best as possible.
Forewarned is forearmed: sharp corners and edges might lead to stress concentrations and ultimately falling parts, whereas undercuts & intricate features bring difficulty with mold production, so consider these matters during calculations before anything else.
Cost Comparison: Low Volume vs. High Volume Injection Molding
Comparing costs between low and high-volume injection molding is complicated, incorporating several facets. For smaller production runs, low-volume injection molding provides a more cost-effective solution, as pricey tooling isn’t necessarily needed.
However, the price per part generally goes up with increased output in this method, while it tends to stay steady or decrease with higher volumes using high-volume injection molding instead.
Things like the complexity of the product at hand, the type of material used, plus the number of cavities in the original fabricating cast have an effect on the financial aspect when low volume is chosen. More intricately designed objects needing widespread access within their molds will call for more significant time and resources – upping costs; particular materials might take exceptional management or even be pricier than standard selections, driving fees up further.
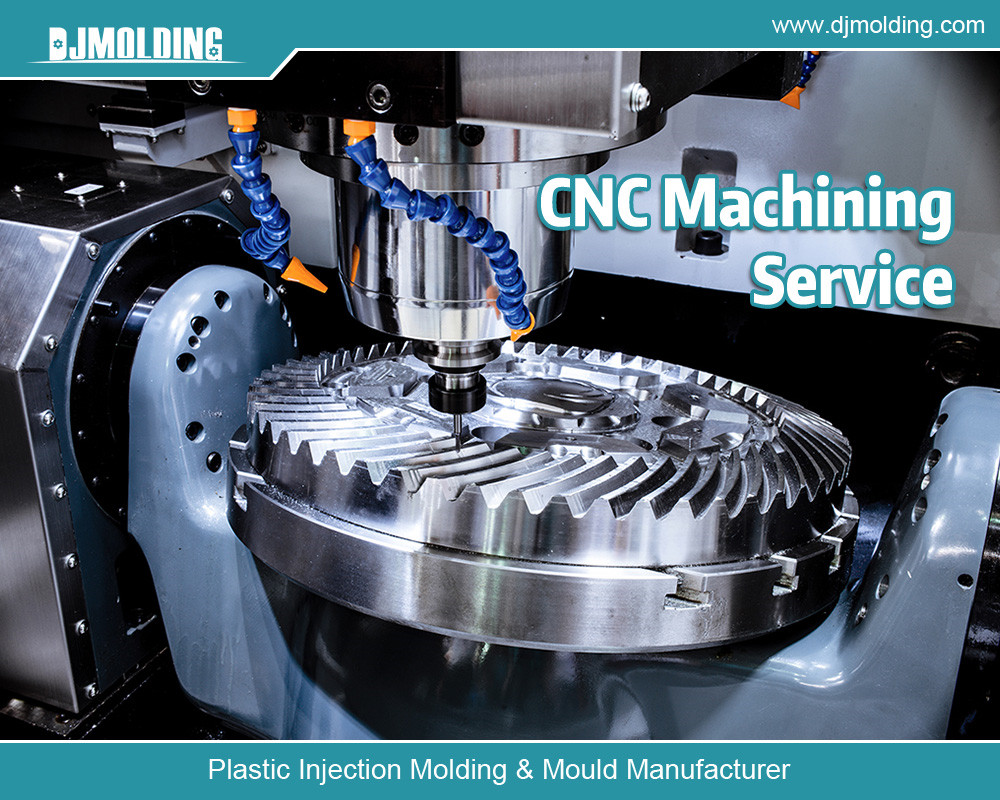
Conclusion
Low-volume injection molding is a wallet-friendly and proficient way to deliver smaller batches of plastic pieces. It packs tons of benefits: cost savings, fast turnaround times, excellent components with tight accuracy levels, plus easy alterations to the design. By sizing up the correct materials and aligning all their manufacturing requirements with the right builder, companies can capitalize on low-volume injection molding fruitfully. What’s more, as technology progresses, so will its future – new resources, tools, and techniques being developed roll out even greater efficiency and grade quality when using such a process.
For more about what is low volume injection molding,you can pay a visit to Djmolding at https://www.djmolding.com/low-volume-injection-molding/ for more info.