What Is The Minimum Quantity For Injection Molding?
What Is The Minimum Quantity For Injection Molding?
Injection molding is the manufacturing process of choice when it comes to producing plastic parts and products fast. It boasts superior efficiency, cost-effectiveness, and a level of precision that consistently delivers complex shapes with pinpoint accuracy. However, those who choose injection molding as their go-to have to be aware of one thing: minimum quantity requirements – an essential element if you want your production project to make economic sense.
As far as minimum quantity needs are concerned, there’s no fixed law. This requirement varies according to material type, machine capacity, volume being produced, and even the design molded onto the final product. Knowing all this helps guide the right way forward; by conceiving a well-thought-out plan in advance and meeting its criteria, producers can look forward optimistically while expecting favorable outcomes through economic savings.
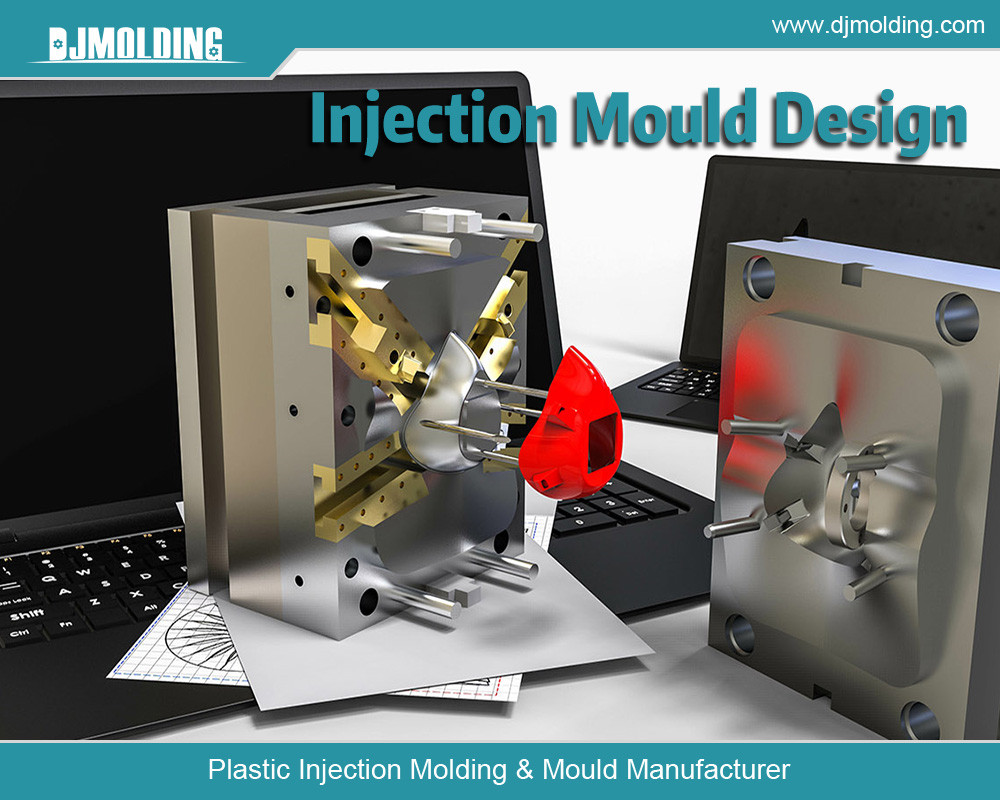
Understanding Minimum Quantity Requirements
Achieving the minimum quantity is critical for making injection molding projects economically feasible. It’s a careful balancing act between material costs, machine setup time, efficiency, and any other cost-associated factors to arrive at that number, which manufacturers absolutely have to hit if they want to break even.
The stakes are high – if production yields fall below the limited amount set by these critical measurements, it could mean spending more cash per part or product than being able to turn a profit. But with just enough attention to detail and management of their resources, producers can ultimately optimize their output process while considerably lessening expenditures in the long run.
Factors Affecting Minimum Quantity for Injection Molding
Several contributory causes can affect the rock-bottom quantity demands for injection molding – ranging from material type and properties to mold design complexity, machine capacity, and capability all the way up to product volume and timetable.
Talking traits, certain materials can be much pricier or necessitate particular handling, which naturally ups the total cost of production. Moreover, some substances have noteworthy peculiarities that require intricate molds or more prolonged extension procedures – inevitably escalating minimal amount specifications.
Molds with finer details may stretch out time frames while ramping up resource consumption, thus inflating the minimal number required to make it all economically practicable. On other occasions, when silhouettes are plainer, production times become shorter while costs per part deflate accordingly.
It’d equally pay off to take into account equipment size specs along with their respective limits because they do cause an effect on productivity performance as well as single component expenses.
Last but not least, big bulks tend to diminish unit prices, while tighter deadlines may pressure costs by requiring higher impact portions in order for operations to flow smoother, plus purse strings to stay untightened.
How to Determine the Minimum Quantity for Injection Molding
Figuring out the exact amount you’ll need for a successful injection molding job can be tricky! To help there are two main ways to figure it out.
First, you can do some calculations. You have to look at things like material cost, machine setup time, production efficiency, and what sort of profit margin you’re working with – basically crunching all the numbers so that making it happen is still financially feasible.
But if those equations go way over your head? Then, talking to someone more experienced in this field is definitely your best bet—experts will know how much your specific project needs since they have tons of industry knowledge and expertise!
Either way, though – knowing just how much product you have to make before reaching financial viability isn’t something that can be easily done.
Benefits of Meeting Minimum Quantity Requirements
Meeting the minimum quantity requirements in injection molding packs a punch, providing manufacturers with three benefits: cost savings to make their wallets swell, improved production efficiency to really boost productivity, and consistent quality control of each part or product that’ll have everyone blown away.
Cost savings is king when it comes down to meeting the minimum. Achieving more significant numbers decreases the individual costs for each part while offering better economy-of-scale deals in the long term – translating into big bucks saved!
Achieving significant quantities really turns up output as well. It optimizes production so changeover and setup times are cut like a knife, making more room for oodles of productivity instead.
Moreover, consistently high quality can be secured by amassing more significant amounts during manufacturing processes. This helps ensure that every single piece makes a grade since rigorous quality control measures become available of this neat higher number trick – giving consistency everywhere you turn.
Challenges of Meeting Minimum Quantity Requirements
Meeting the minimum quantity requirements in injection molding comes with nothing but advantages, yet some significant challenges are lurking behind. Between a heftier initial investment, drawn-out lead times, and curtailed design flexibility, making sure you meet the criteria isn’t always easy.
Let’s begin with the higher initial investment required of larger quantities – more materials, machine time, and resources equal to more considerable upfront costs! So, before you commit to anything substantial here, make sure your budget is in check.
On top of that, lengthy lead times can pose quite a problem; setups plus production plus quality control all take up considerable time, which won’t always fit into tight deadlines or specific demands – so do keep these considerations in mind when planning and managing what needs doing.
Finally, we have limited design flexibility: one has to look at standardized molds or designs often if one wants their production process to be effective.
This may leave manufacturers somewhat high and dry when faced with projects requiring custom designs – such is something to ponder ahead of committing yourself too fully here.
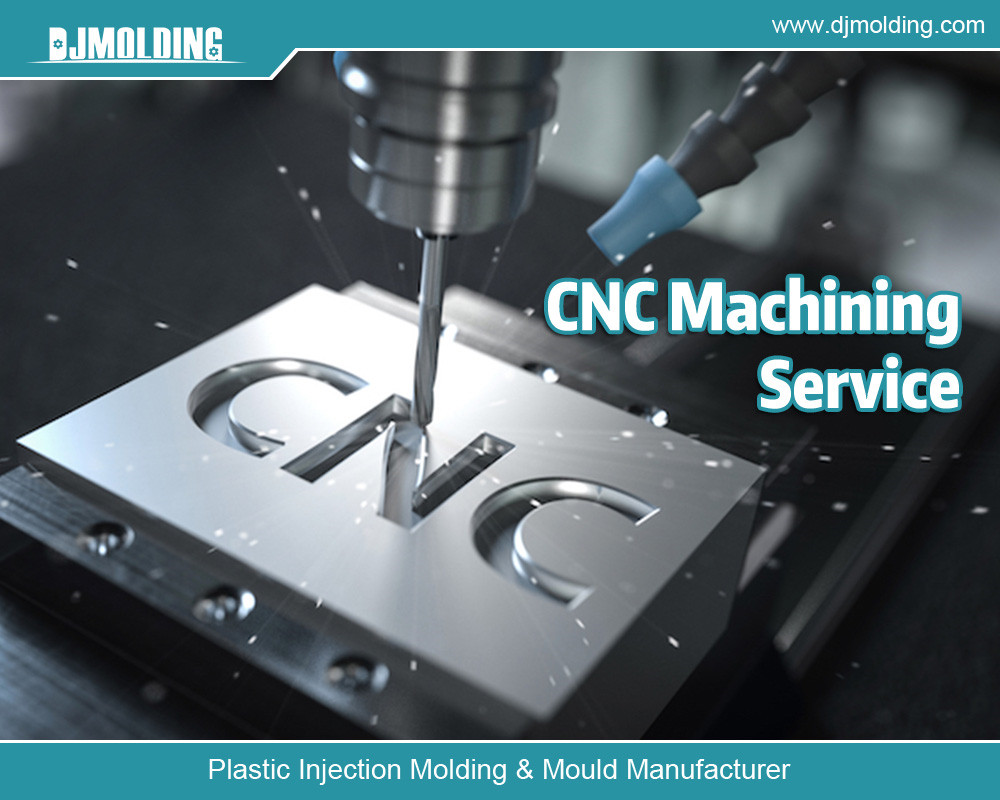
Conclusion
sticking to the minimum quantity requisites is a total must for successful injection molding projects. You have to make sure you properly assess your material type, mold design, machine capacity, and output volume – that way, you can find out what amount will be needed for the process to really pull through economically.
Not only does meeting these standards mean cost efficiencies and efficiency of production processes, but also, quality is ensured! Fair warning, though – there are specific challenging tasks like increased initial investment, extended lead times, and limited leeway with design choices ahead of manufacturers undertaking this task. So, if they bear those circumstances in mind and try alternative ways of creation, then bang on! They’d be able to neatly optimize their production paths towards glorious success with injection molding projects.
For more about what is the minimum quantity for injection molding,you can pay a visit to Djmolding at https://www.djmolding.com/about/ for more info.