3D Printing vs Injection Molding: A Comprehensive Comparison
3D Printing vs Injection Molding: A Comprehensive Comparison
The manufacturing landscape has undergone significant transformations in recent decades, with technological advancements introducing innovative methods such as 3D printing and injection molding. These two techniques are pivotal in modern manufacturing, offering unique advantages and applications. This article provides a detailed comparison of 3D printing and injection molding, examining their processes, benefits, limitations, cost considerations, environmental impact, and prospects.
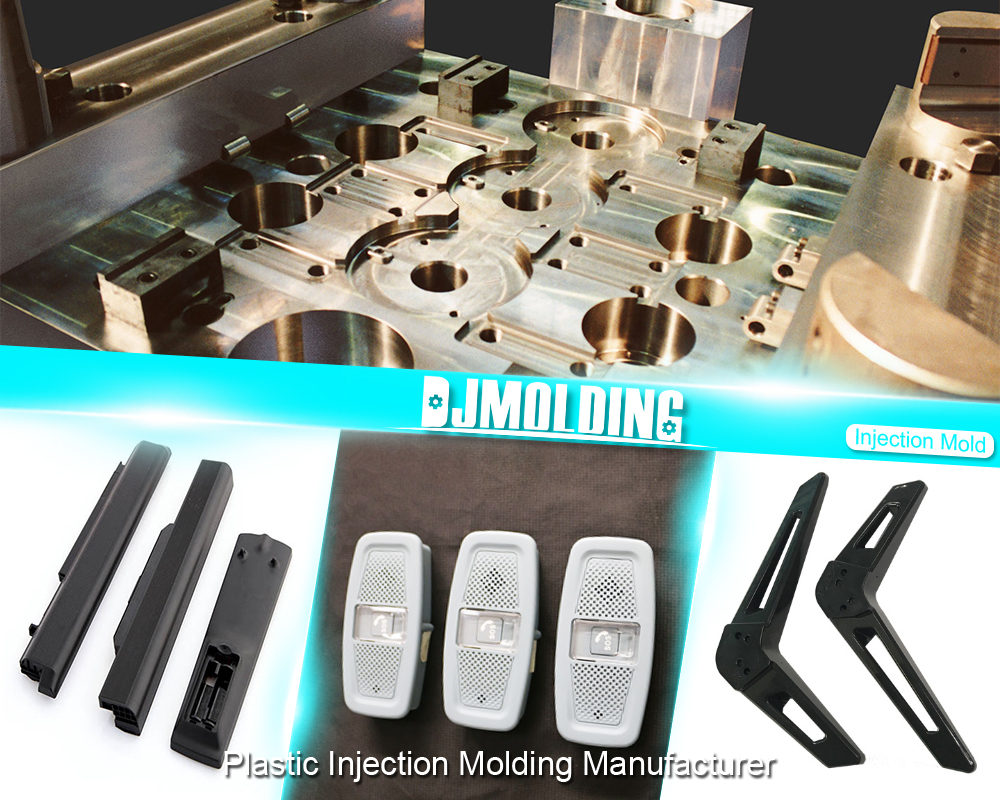
Overview of 3D Printing
What is 3D Printing?
3D Printing, also known as additive manufacturing, is a process that creates three-dimensional objects by layering materials based on digital models. This technology allows for producing complex geometries that are difficult or impossible to achieve with traditional manufacturing methods.
How Does 3D Printing Work?
The 3D printing process typically involves the following steps:
- Design Creation: Using CAD (Computer-Aided Design) software, a digital model of the object is created.
- Slicing: The digital model is sliced into thin layers, which will be printed sequentially.
- Printing: The 3D printer deposits material layer by layer, following the sliced model’s instructions.
- Post-Processing: The printed object may require additional finishing steps such as sanding, painting, or curing.
Types of 3D Printing Technologies
There are several types of 3D printing technologies, each with distinct characteristics:
- Fused Deposition Modeling (FDM): This is the most common type, using thermoplastic filaments that are melted and extruded through a nozzle.
- Stereolithography (SLA): Uses a laser to cure liquid resin into solid layers.
- Selective Laser Sintering (SLS): Utilizes a laser to sinter powdered material, binding it together to create a solid structure.
- Digital Light Processing (DLP) is similar to SLA. It uses a digital projector screen to flash a single image of each layer simultaneously.
Overview of Injection Molding
What is Injection Molding?
Injection molding is a manufacturing process that produces large volumes of parts by injecting molten material into a mold. This method is highly efficient for mass-producing identical items.
How Does Injection Molding Work?
The injection molding process involves several key steps:
- Mold Design: A mold, usually made from metal, is designed to the specifications of the desired part.
- Material Melting: Plastic pellets are melted into a molten state.
- Injection: The molten plastic is injected into the mold cavity under high pressure.
- Cooling: The mold is cooled, solidifying the plastic into the shape of the part.
- Ejection: The finished part is ejected from the mold.
Types of Materials Used in Injection Molding
Injection molding primarily uses thermoplastics, but other materials like metals, glass, and elastomers can also be used. Common plastics include:
- Polyethylene (PE)
- Polypropylene (PP)
- Acrylonitrile Butadiene Styrene (ABS)
- Polycarbonate (PC)
Critical Differences Between 3D Printing and Injection Molding
Production Speed and Volume
3D Printing:
- Ideal for low-volume production and prototyping.
- Slower production speed as each layer is printed sequentially.
- Suitable for producing complex, customized, or one-off parts.
Injection Molding:
- Best suited for high-volume production.
- Fast production cycle once the mold is created.
- Efficient for producing large quantities of identical parts.
Design Flexibility
3D Printing:
- High design flexibility, allowing for complex geometries and intricate details.
- Easy to modify designs without additional tooling costs.
- Supports rapid iteration and testing of new designs.
Injection Molding:
- Limited by mold design, making changes costly and time-consuming.
- Best for simple to moderately complex parts.
- Mold creation can be a lengthy and expensive process.
Material Selection
3D Printing:
- Wide range of materials, including various plastics, metals, ceramics, and composites.
- Material properties can vary significantly between different 3D printing technologies.
- There are some limitations in material strength and durability compared to injection molding.
Injection Molding:
- Extensive range of materials with well-established properties and performance.
- Materials used in injection molding generally offer superior mechanical properties.
- Suitable for parts requiring high strength, durability, and specific material characteristics.
Cost Considerations
3D Printing:
- Lower initial setup costs, making it cost-effective for small runs and prototyping.
- Higher per-unit cost for large-scale production compared to injection molding.
- Economical for custom or complex parts with low production volumes.
Injection Molding:
- High initial tooling and mold-making costs can be a barrier for small production runs.
- Low per-unit cost for high-volume production, making it cost-effective for large quantities.
- Economies of scale significantly reduce overall production costs as volume increases.
Applications and Use Cases
3D Printing Applications
3D Printing is widely used across various industries for applications such as:
- Prototyping: Rapid prototyping of new products and components.
- Medical Devices: Custom prosthetics, implants, and surgical tools.
- Aerospace: Lightweight and complex components for aircraft and spacecraft.
- Consumer Goods: Customizable products like jewelry, fashion accessories, and home decor.
- Automotive: Custom parts, tooling, and prototyping.
Injection Molding Applications
Injection molding is commonly used in industries requiring mass production of parts, including:
- Automotive: High-volume production of parts like dashboards, bumpers, and interior components.
- Electronics: Casings, connectors, and various plastic components.
- Consumer Goods: Household items, toys, and packaging materials.
- Medical Devices: Syringes, vials, and other disposable medical products.
- Industrial Components: Gears, bearings, and enclosures.
Environmental Impact
3D Printing
- Material Efficiency: 3D Printing generates minimal waste, using only the necessary material to create the part.
- Energy Consumption: Generally lower energy consumption compared to traditional manufacturing methods.
- Recyclability: Many 3D-printed materials can be recycled, but the process can be complex and material-dependent.
Injection Molding
- Material Waste: Injection molding can produce significant material waste, particularly during the initial setup and tuning of the mold.
- Energy Consumption: High energy consumption due to the heating and cooling cycles required for the process.
- Recyclability: Thermoplastics used in injection molding are highly recyclable, and waste can often be reprocessed and reused.
Future Prospects and Trends
3D Printing Advancements
- Material Development: Ongoing research expands the range of printable materials with improved properties.
- Speed and Precision: Advances in technology are increasing printing speeds and precision, making 3D Printing more competitive for larger production runs.
- Integration with Traditional Manufacturing: Hybrid manufacturing systems that combine 3D Printing with traditional methods are emerging, offering the best of both worlds.
Injection Molding Innovations
- Automated Systems: Increasing automation in injection molding is improving efficiency and reducing labor costs.
- Advanced Materials: The development of new materials with enhanced properties is expanding injection molding applications.
- Sustainability: Efforts to reduce environmental impact include using bio-based plastics and improving recycling processes.
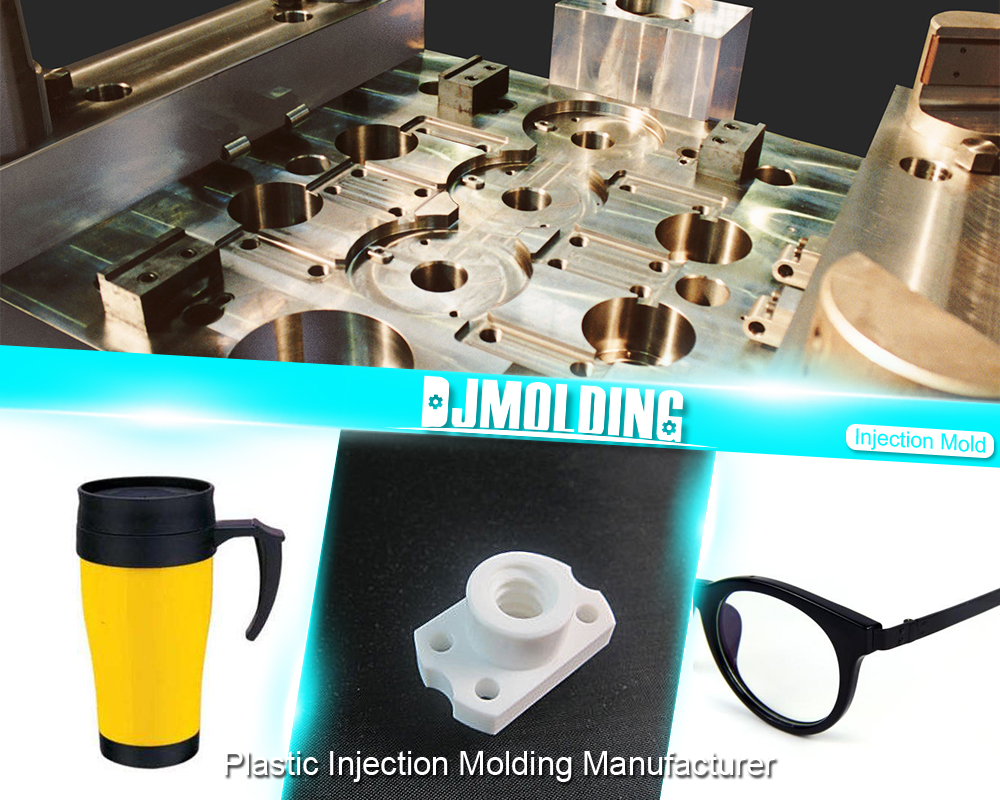
Conclusion
3D printing and injection molding are vital manufacturing techniques with distinct advantages and limitations. 3D Printing excels in design flexibility, customization, and low-volume production, making it ideal for prototyping and complex parts. Injection molding, on the other hand, is highly efficient for mass production, offering low per-unit costs and superior material properties for high-volume manufacturing.
Understanding the strengths and weaknesses of each method is crucial for selecting the appropriate manufacturing technique based on specific project requirements, production volume, and budget considerations. As technology evolves, 3D printing and injection molding will likely see further advancements, broadening their applications and enhancing their capabilities in the manufacturing industry.
For more about 3d printing vs injection molding: a comprehensive comparison,you can pay a visit to Djmolding at https://www.djmolding.com/ for more info.