How Liquid Silicone Rubber Injection Molding Process Is Revolutionizing Automotive Plastic Parts Manufacturing
How Liquid Silicone Rubber Injection Molding Process Is Revolutionizing Automotive Plastic Parts Manufacturing
Rev up your engines and get ready for a game-changing revolution in automotive manufacturing! LSR (also called Liquid Silicone Rubber) Injection Molding is taking the industry by storm and leaving traditional processes in the rearview mirror. By combining the best of both worlds – liquid and solid materials – this cutting-edge technology is paving the way for improved performance, durability and efficiency in automotive parts. Join us as we explore how LSR is shaping the future of automotive production.
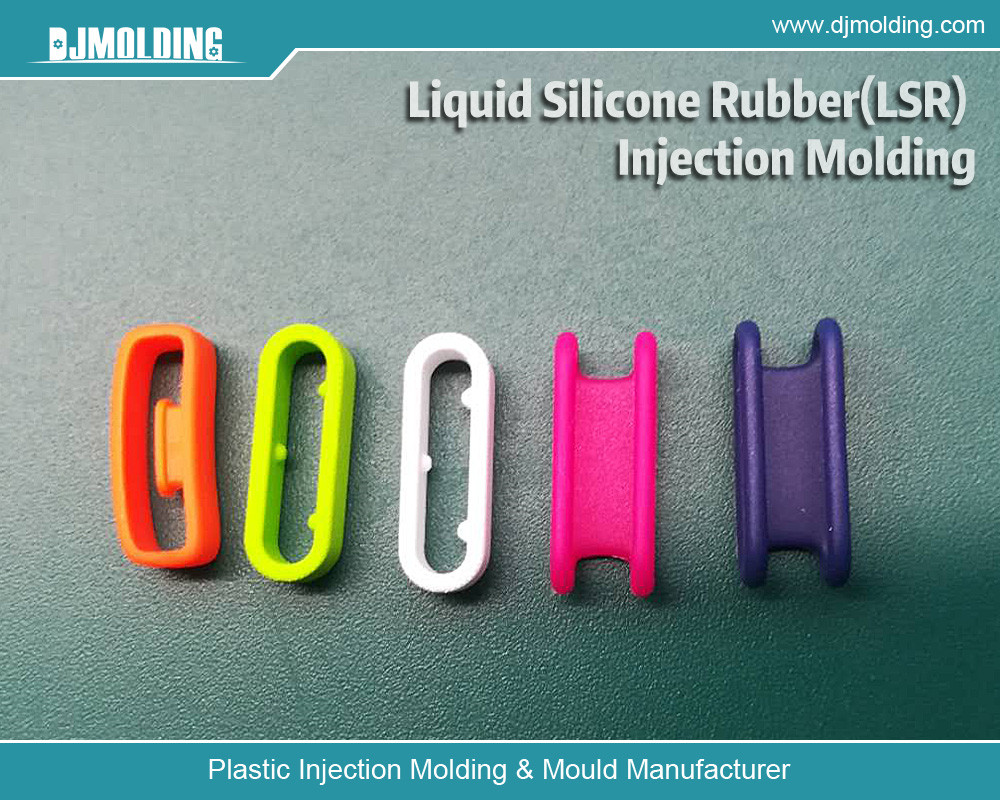
Advantages of LSR Injection Molding in Automotive Manufacturing
There are several advantages to using LSR injection molding in automotive manufacturing. These include:
High precision and accuracy: LSR molding allows for highly precise and accurate parts to be produced with ease. This is because the liquid silicone rubber can be injected into the mold with a high degree of accuracy, resulting in parts that are consistent in size and shape.
Faster production time: LSR molding is a fast and efficient process that allows for large quantities of parts to be produced quickly. This is because the liquid silicone rubber can be injected into the mold at a high rate of speed, resulting in faster production times.
Improved part quality and consistency: LSR molding produces parts that are consistent in size, shape, and quality. This is because the liquid silicone rubber can be injected into the mold with a high degree of accuracy, resulting in parts that are free from defects and inconsistencies.
Reduced waste and scrap: LSR molding produces very little waste and scrap, as the liquid silicone rubber can be injected into the mold with a high degree of accuracy. This results in a more efficient and cost-effective manufacturing process.
Enhanced design flexibility: LSR molding allows for complex designs and shapes to be created with ease. This is because the liquid silicone rubber can be injected into the mold with a high degree of accuracy, resulting in parts that are consistent in size and shape.
LSR Injection Molding vs. Traditional Rubber Molding
There are several differences between LSR molding and traditional rubber molding. These include:
Materials: LSR molding uses liquid silicone rubber, while traditional rubber molding uses solid rubber.
Process: LSR molding involves injecting liquid silicone rubber into a mold, while traditional rubber molding involves compressing solid rubber into a mold.
Precision: LSR molding allows for higher precision and accuracy than traditional rubber molding.
Advantages of LSR Injection Molding over Traditional Rubber Molding
There are several advantages to using LSR molding over traditional rubber molding. These include:
Higher precision and accuracy: LSR molding allows for higher precision and accuracy than traditional rubber molding, resulting in parts that are consistent in size and shape.
Faster production time: It is a faster and more efficient process than traditional rubber molding, resulting in faster production times.
Improved part quality and consistency: It produces parts that are consistent in size, shape, and quality, resulting in parts that are free from defects and inconsistencies.
Reduced waste and scrap: It produces very little waste and scrap, resulting in a more efficient and cost-effective manufacturing process.
Enhanced design flexibility: It allows for complex designs and shapes to be created with ease, resulting in parts that are more aesthetically pleasing and functional.
Applications of LSR Injection Molding in Automotive Industry
There are several applications of LSR injection molding in the automotive industry. These include:
Seals and gaskets: LSR molding is commonly used to produce seals and gaskets for automotive applications. These parts are highly durable and resistant to wear and tear, making them ideal for use in automotive engines and transmissions.
Electrical components: It is also used to produce electrical components for automotive applications. These parts are highly resistant to heat and chemicals, making them ideal for use in automotive wiring and connectors.
Interior components: It is also used to produce interior components for automotive applications, such as dashboard panels and door handles. These parts are highly durable and resistant to wear and tear, making them ideal for use in high-traffic areas of the vehicle.
How LSR Injection Molding Improves Automotive Part Performance
LSR injection molding can improve the performance of automotive parts in several ways. These include:
Improved durability and resistance to wear and tear: LSR injection molding produces parts that are highly durable and resistant to wear and tear, resulting in parts that last longer and require less maintenance.
Enhanced heat and chemical resistance: LSR injection molding produces parts that are highly resistant to heat and chemicals, making them ideal for use in high-temperature and high-chemical environments.
Better sealing and insulation properties: LSR injection molding produces parts that have better sealing and insulation properties, resulting in parts that are more effective at preventing leaks and reducing noise.
Cost Benefits of LSR Injection Molding in Automotive Manufacturing
There are several cost benefits to using LSR injection molding in automotive manufacturing. These are:
Lower production costs: LSR injection molding is a more efficient and cost-effective process than traditional rubber molding, resulting in lower production costs.
Reduced labor costs: LSR injection molding requires less labor than traditional rubber molding, resulting in reduced labor costs.
Increased efficiency and productivity: LSR injection molding is a faster and more efficient process than traditional rubber molding, resulting in increased efficiency and productivity.
LSR Injection Molding and Sustainability in Automotive Industry
LSR injection molding can also have a positive impact on sustainability in the automotive industry. They could be:
Reduced environmental impact: LSR injection molding produces very little waste and scrap, resulting in a more environmentally friendly manufacturing process.
Use of recyclable materials: LSR injection molding uses silicone-based materials that are recyclable, resulting in a more sustainable manufacturing process.
Energy efficiency: LSR injection molding is a more energy-efficient process than traditional rubber molding, resulting in a more sustainable manufacturing process.
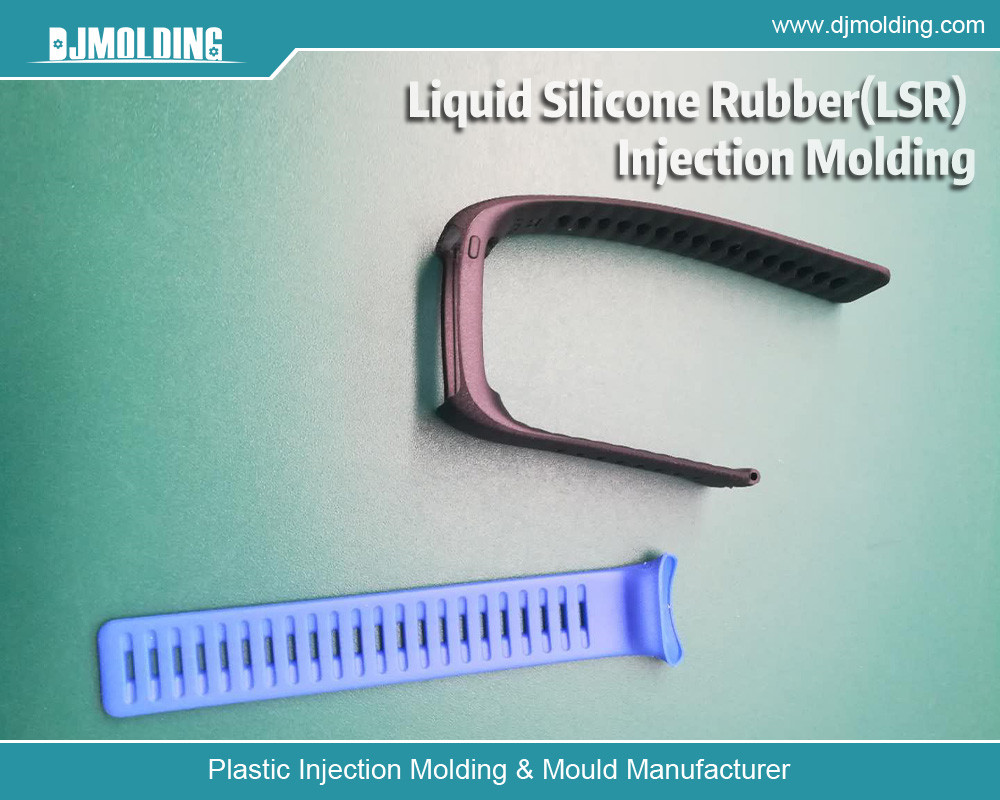
Final Thoughts
In conclusion, it is evident that Liquid Silicone Rubber Injection Molding is transforming the automotive industry. The technology provides manufacturers with numerous advantages such as reduced production costs, enhanced product quality, and improved efficiency. As the demand for high-performance automotive components continues to grow, LSR injection molding is proving to be a reliable solution to meet these needs.
For more about how liquid silicone rubber injection molding process is revolutionizing automotive plastic parts manufacturing,you can pay a visit to Djmolding at https://www.djmolding.com/liquid-silicone-rubberlsr-injection-molding/ for more info.