The Advantages Of Liquid Silicone Rubber Injection Molding Process For Consumer Products
The Advantages Of Liquid Silicone Rubber Injection Molding Process For Consumer Products
As consumer demand for high-quality, durable products continues to grow, manufacturers are turning to innovative materials and production methods to meet these needs. LSR injection molding is one such method that has gained popularity in recent years. LSR is a versatile material that offers a range of benefits for consumer products, including superior durability, resistance to extreme temperatures, and excellent fluidity for intricate designs.
Today, we will explore the benefits of LSR injection molding for consumer products and how it can help manufacturers meet the demands of today’s discerning consumers.
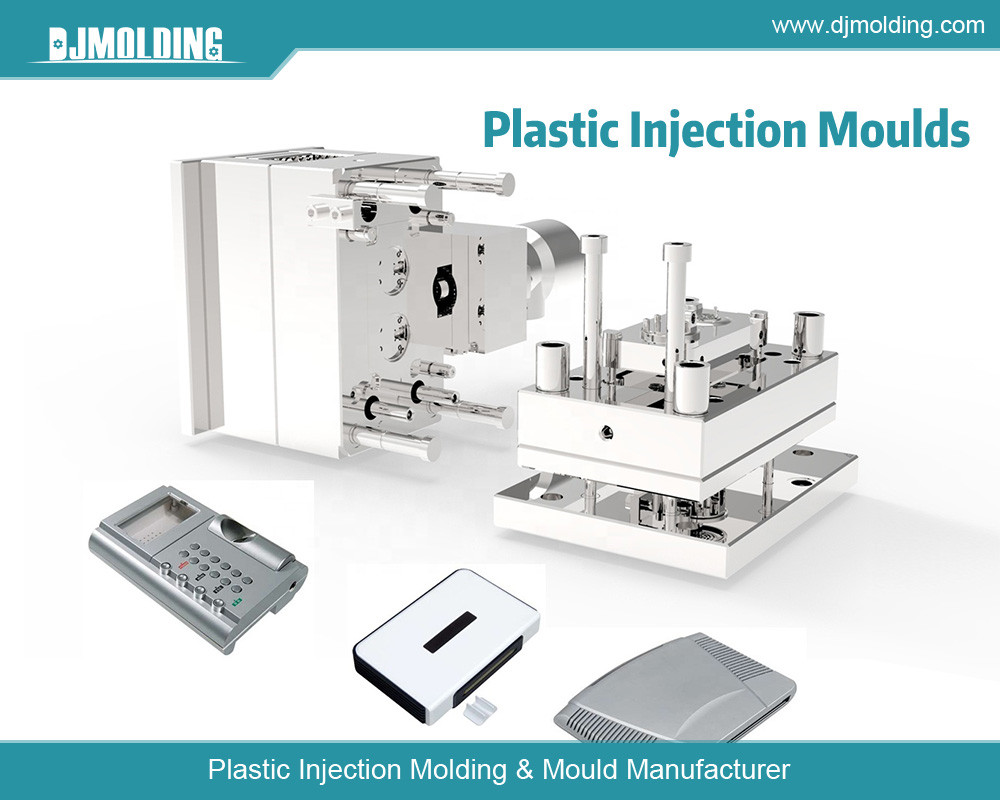
What is LSR Injection Molding?
LSR Molding is a manufacturing process that involves injecting liquid silicone rubber into a mold to produce a wide range of consumer products. This process is widely used in the production of medical devices, baby products, kitchenware, electronics, and automotive parts. LSR Injection Molding is known for its durability, flexibility, precision, and cost-effectiveness. In this article, we will explore the advantages of LSR Injection Molding for consumer products, its applications, and the future of this technology.
Advantages of LSR Molding for Consumer Products
Durability and Longevity of LSR Products: LSR Injection Molding produces products that are highly durable and long-lasting. LSR products are resistant to extreme temperatures, chemicals, and UV radiation. They are also waterproof and can withstand harsh environments. This makes LSR products ideal for use in medical devices, automotive parts, and electronics.
Flexibility and Versatility of LSR Injection Molding: the process of LSR Injection Molding is highly flexible and versatile. It can produce products of different shapes, sizes, and colors. This makes it possible to create complex designs and intricate parts. LSR Injection Molding can also produce products with different levels of hardness and softness, making it ideal for use in baby products and medical devices.
Precision and Consistency in LSR Manufacturing: LSR Molding is highly precise and consistent manufacturing. It produces products with tight tolerances and high accuracy. This makes it possible to produce products that meet strict quality standards. LSR Injection Molding also produces products with consistent properties, ensuring that each product is of the same quality.
Cost-Effective Production with LSR Injection Molding: LSR Molding happens to be a cost-effective manufacturing process. It requires less labor and produces less waste than other manufacturing processes. This makes it possible to produce products at a lower cost. LSR Injection Molding also produces products with a longer lifespan, reducing the need for frequent replacements.
Environmental Benefits of LSR Injection Molding: LSR Molding is an environmentally friendly manufacturing process. It produces less waste than other manufacturing processes and uses less energy. This reduces the carbon footprint of the manufacturing process and helps to protect the environment.
Applications of LSR Injection Molding in Consumer Products
Medical Devices: LSR Molding is widely used in the production of medical devices. LSR products are biocompatible, meaning they do not cause any harm to the human body. This makes LSR products ideal for use in medical devices such as catheters, pacemaker leads, and surgical instruments.
Baby Products: LSR Molding is also used in the production of baby products. LSR products are soft and flexible, making them ideal for use in baby bottles, pacifiers, and teething toys. LSR products are also easy to clean and sterilize, ensuring that they are safe for use by babies.
Kitchenware: LSR Molding is used in the production of kitchenware such as baking mats, oven mitts, and spatulas. LSR products are heat-resistant and can withstand high temperatures, making them ideal for use in the kitchen.
Electronics: It is used in the production of electronics such as phone cases, earbuds, and smartwatch bands. LSR products are durable and can withstand the wear and tear of daily use. They are also waterproof, protecting electronics from water damage.
Automotive Parts: It is used in the production of automotive parts such as gaskets, seals, and hoses. LSR products are resistant to extreme temperatures and chemicals, making them ideal for use in the automotive industry.
Future of LSR Injection Molding in Consumer Products
Advancements in LSR technology: The LSR Molding industry has come a long way since its inception, and with each passing year, new advancements in technology are being made that are revolutionizing the way products are manufactured. These advancements have made it possible to produce products with even greater precision, consistency, and durability than ever before.
One of the most significant advances in recent years has been the development of liquid silicone rubber, which has become the material of choice for many manufacturers due to its superior properties. LSR is highly resistant to heat, chemicals, and UV radiation, making it ideal for use in a wide range of applications.
Additionally, LSR molding machines have become more sophisticated and efficient, allowing for faster production times and greater accuracy in the manufacturing process. With these advancements, the LSR Injection Molding industry is poised to continue growing and evolving in the years to come.
LSR products are becoming increasingly popular among consumers due to their numerous benefits. These benefits include their durability, flexibility, and resistance to extreme temperatures and chemicals. As a result, the demand for LSR products is growing rapidly, which is driving the growth of the LSR Injection Molding industry.
More and more companies are now looking to produce LSR products to meet this rising demand. This has led to an increase in the number of manufacturers specializing in LSR Injection Molding, as well as an increase in the variety of LSR products available in the market. With the continued growth of the LSR Injection Molding industry, it is expected that even more innovative LSR products will be developed in the future to meet the evolving needs of consumers.
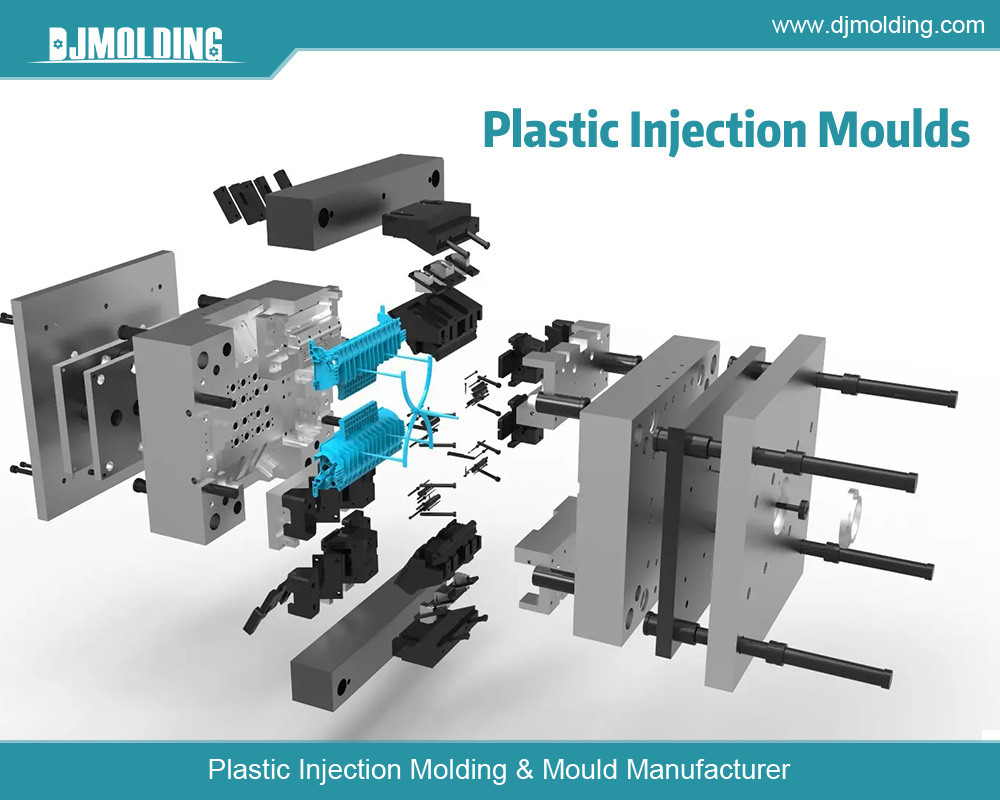
Conclusion: Why LSR Injection Molding is the Best Choice for Consumer Product
LSR Molding is a highly versatile, precise, and cost-effective manufacturing process that produces durable, flexible, and environmentally friendly products. LSR Injection Molding is widely used in the production of medical devices, baby products, kitchenware, electronics, and automotive parts. The future of LSR Injection Molding looks bright, with new advancements in technology and growing demand for LSR products. When it comes to choosing the right manufacturing process for consumer products, LSR Injection Molding is the best choice.
For more about the advantages of liquid silicone rubber injection molding process for consumer products,you can pay a visit to Djmolding at https://www.djmolding.com/liquid-silicone-rubberlsr-injection-molding/ for more info.