What Is The Difference Of Die Casting Vs Injection Molding
What Is The Difference Of Die Casting Vs Injection Molding
Die casting and injection molding are two popular manufacturing processes used to produce a wide range of products. Understanding the differences between these two processes is crucial for manufacturers and designers in order to make informed decisions about which method is best suited for their specific needs.
Die casting involves the use of a metal mold, or die, into which molten metallic material is injected under high pressure. The metal solidifies within the mold, creating a precise and detailed final product. Injection molding, on the other hand, utilizes a similar concept but with the use of thermoplastic materials. Molten plastic is injected into a mold, where it cools and solidifies to form the desired shape.
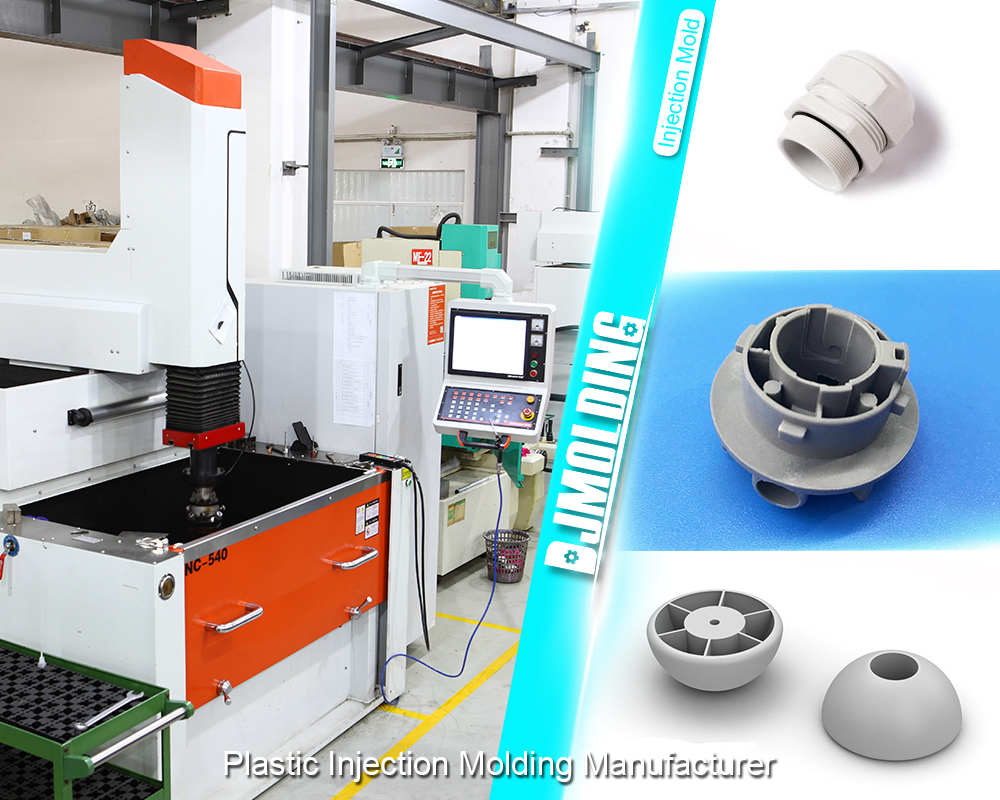
The Process of Die Casting
The die casting process begins with the creation of a mold, typically made from steel or other durable materials. This mold is then mounted onto a machine that injects molten metal into it at high pressure. The metal fills the mold cavity and takes on its shape as it cools and solidifies. Once the metal hardens, the mold is opened and the finished product is removed.
There are several types of die casting methods, including hot chamber die casting’ and cold chamber die casting’. Hot chamber die casting is used for metals that have low melting point, like zinc and magnesium, while cold chamber die casting’ is used for metals with higher melting points, such as aluminum and copper.
Advantages of die casting include its ability to produce complex shapes with high precision and accuracy. Additionally, die casting allows for the production of parts with thin walls and intricate details. However, die casting can be expensive due to the cost of creating and maintaining the molds.
The Process of Injection Molding
Injection molding follows a similar process to die casting but uses thermoplastic materials instead of metals. The process begins with the creation of a mold, typically made from steel or aluminum. The mold is then mounted onto an injection molding machine, which injects molten plastic into the mold at high pressure. The plastic cools and solidifies within the mold, taking on its final shape.
There are various types of injection molding methods, including conventional injection molding, insert molding, and overmolding. Conventional injection molding is the most common method and involves injecting molten plastic into a single cavity mold. Insert molding involves the insertion of pre-formed components into the mold before injection, while overmolding involves the use of multiple materials to create a single part.
Advantages of injection molding include its ability to produce complex shapes with high precision and repeatability. Injection molding also allows for the production of parts with a wide range of sizes and geometries. However, the initial cost of creating the molds can be high, especially for complex designs.
Materials Used in Die Casting and Injection Molding
In die casting, common materials used include aluminum, zinc, magnesium, and copper alloys. These materials offer excellent strength and durability, making them suitable for various applications. Aluminum is particularly popular due to its lightweight properties and corrosion resistance.
In injection molding, thermoplastic materials are used, including polypropylene, polyethylene, polystyrene, and ABS. These materials offer a wide range of properties, such as flexibility, impact resistance, and chemical resistance. Thermoplastics can also be easily recycled, making them more environmentally friendly compared to metals used in die casting.
When comparing materials used in die casting and injection molding, it is important to consider factors such as strength, weight, cost, and specific application requirements. Each process has its own set of materials that are best suited for optimal performance.
Advantages of Die Casting over Injection Molding
Die casting offers several advantages over injection molding in certain applications. One key advantage is the strength and durability of die cast parts. The use of metals in die casting allows for the production of parts that can withstand high loads and harsh environments. Additionally, die casting provides excellent surface finish, with the ability to achieve smooth and polished surfaces.
Another advantage of die casting is its ability to achieve tight tolerances and high precision. The metal molds used in die casting allow for the production of parts with intricate details and complex geometries. This makes die casting suitable for applications that require precise dimensions and tight tolerances.
Furthermore, die casting can be cost-effective for large production runs. Once the molds are created, the cost per part decreases significantly as the production volume increases. This makes die casting a viable option for industries that require high-volume production.
Advantages of Injection Molding over Die Casting
While die casting has its advantages, injection molding also offers unique benefits in certain applications. One advantage of injection molding is its flexibility in design. The use of thermoplastic materials allows for greater design freedom, as they can be molded into complex shapes and intricate details. Injection molding also allows for the production of parts with varying wall thicknesses, which can be beneficial in reducing material costs.
Injection molding also offers faster production times compared to die casting. The injection molding process is typically faster, allowing for higher production rates. This makes injection molding suitable for industries that require quick turnaround times and shorter lead times.
Additionally, injection molding generally has lower tooling costs compared to die casting. The molds used in injection molding are typically less expensive to create and maintain, especially for simpler designs. This makes injection molding a more cost-effective option for small to medium-sized production runs.
Furthermore, injection molding allows for the use of a wider range of materials compared to die casting. Thermoplastic materials offer a wide range of properties, allowing manufacturers to choose materials that best suit their specific application requirements.
Quality Comparison between Die Casting and Injection Molding
The quality of parts produced through die casting and injection molding can vary depending on several factors. In die casting, the use of metal molds allows for high precision and accuracy, resulting in parts with tight tolerances and intricate details. Die cast parts also have excellent surface finish, with the ability to achieve smooth and polished surfaces.
In injection molding, the quality of parts is also high due to the precision and repeatability of the process. Injection molding allows for the production of parts with complex shapes and high dimensional accuracy. However, the surface finish of injection molded parts may not be as smooth as die cast parts.
Factors that can affect the quality of both processes include material selection, mold design, process control, and post-processing techniques. It is important to consider these factors when evaluating the quality requirements for a specific application.
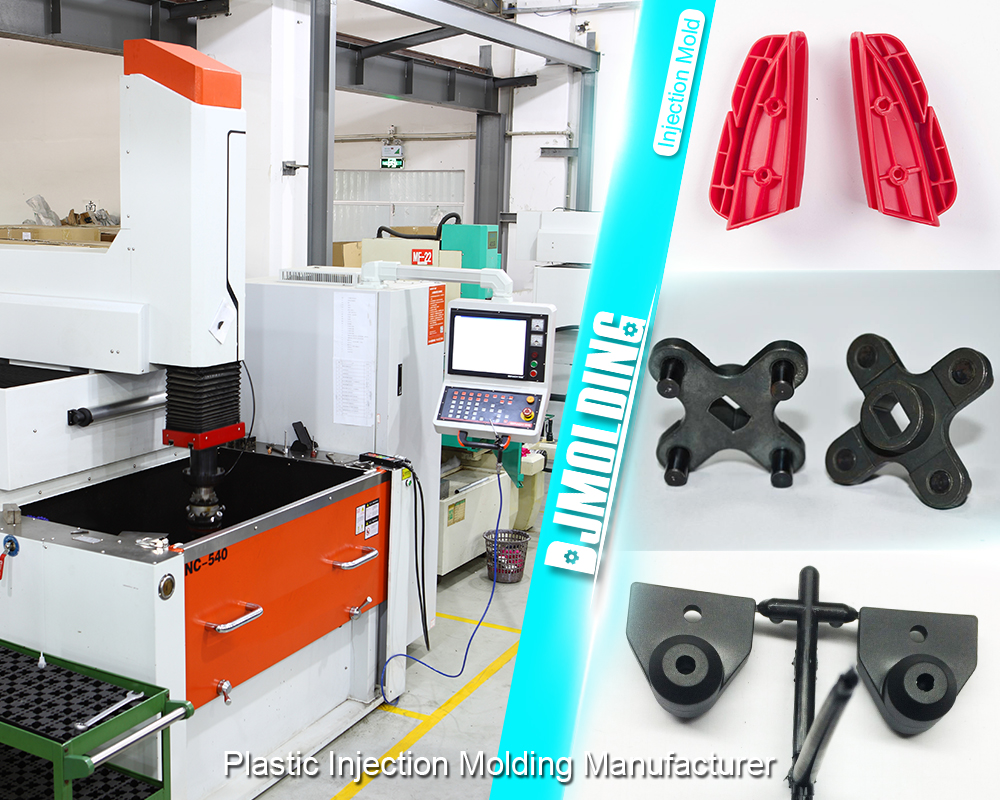
Which is Better – Die Casting or Injection Molding?
In conclusion, both die casting and injection molding have their own set of advantages and disadvantages. The choice between the two processes depends on various factors such as production volume, complexity of design, material requirements, cost considerations, and environmental impact.
Die casting offers strength and durability, excellent surface finish, tight tolerances, and cost-effectiveness for large production runs. It is well-suited for applications that require high load-bearing capabilities and precise dimensions.
Injection molding offers flexibility in design, faster production times, lower tooling costs, and the ability to use a wider range of materials. It is ideal for applications that require complex shapes, quick turnaround times, and a variety of material properties.
Ultimately, the decision between die casting and injection molding should be based on a thorough evaluation of the specific requirements and constraints of each project. By considering factors such as cost, quality, application, and environmental impact, manufacturers and designers can make an informed decision that best suits their needs.
For more about what is the difference of die casting vs injection molding,you can pay a visit to Djmolding at https://www.djmolding.com/aluminum-injection-molding-in-plastic-product-manufacturing/ for more info.